Strategies for Integrated Supply Chain Management
Enhance your supply chain management with integrated strategies focusing on partnerships, technology, visibility, lean principles, and flexibility for optimal efficiency.
SUPPLY CHAIN
The Procure 4 Marketing Team
6/19/20245 min read
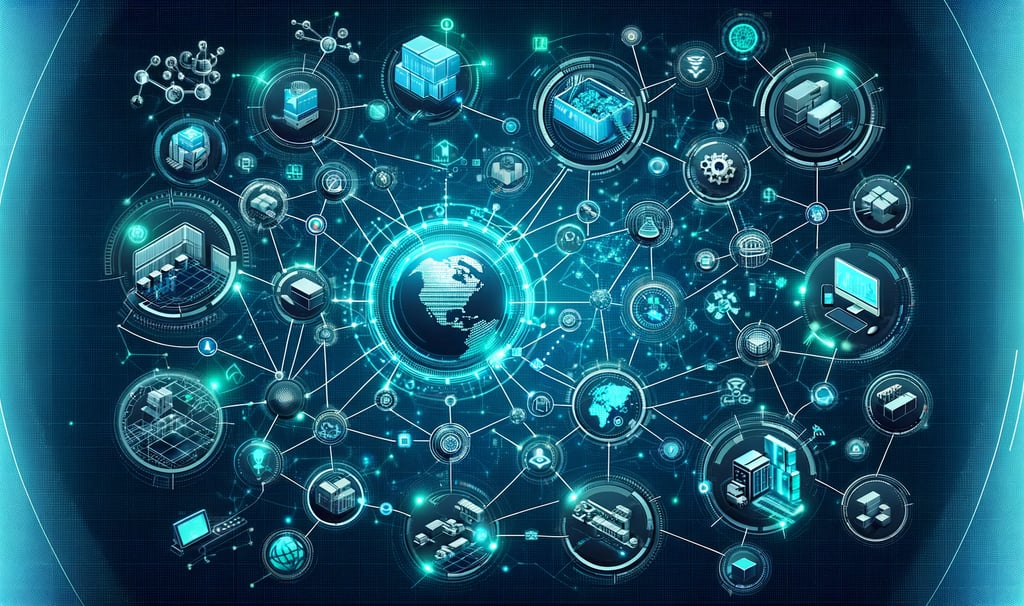
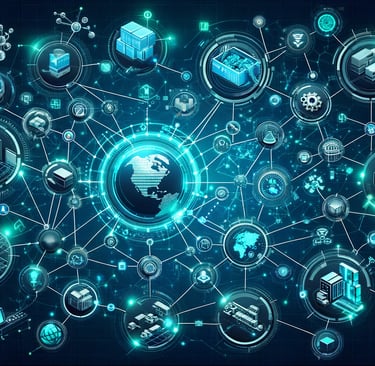
Supply chain integration refers to the coordination and seamless flow of information, goods, and services across various stages of the supply chain, from suppliers to manufacturers to distributors to customers. An integrated supply chain is crucial for businesses aiming to enhance efficiency, reduce costs, and improve customer satisfaction. This post will explore strategies for achieving integrated supply chain management, providing a detailed and friendly guide to help businesses optimize their operations.
Importance of Integrated Supply Chain Management
Integrated supply chain management is vital for several reasons:
Efficiency: Streamlining processes and improving communication across the supply chain can significantly enhance operational efficiency.
Cost Reduction: By optimizing inventory levels and reducing waste, businesses can lower their operational costs.
Customer Satisfaction: Improved visibility and responsiveness ensure that customer needs are met more effectively, enhancing overall satisfaction.
Key Strategies for Supply Chain Integration
1. Establishing Strong Partnerships
Building strong relationships with suppliers, manufacturers, and distributors is essential for supply chain integration. These partnerships foster collaboration and trust, ensuring that all parties are aligned with the same goals.
Tips for Establishing Strong Partnerships:
Regular Communication: Maintain open lines of communication through regular meetings, updates, and collaborative platforms.
Joint Planning: Engage in joint planning sessions to align strategies and objectives.
Performance Metrics: Develop shared performance metrics to track progress and address issues promptly.
2. Leveraging Technology
Technology plays a critical role in integrating supply chains. Implementing advanced technologies such as Enterprise Resource Planning (ERP) systems, IoT devices, and data analytics can enhance visibility and coordination.
Technological Solutions for Integration:
ERP Systems: Integrate various business processes into a single system to streamline operations and improve data accuracy.
IoT Devices: Use IoT sensors for real-time tracking of inventory, shipments, and equipment.
Data Analytics: Employ data analytics to gain insights into supply chain performance and identify areas for improvement.
3. Enhancing Visibility
Visibility across the supply chain is crucial for identifying bottlenecks and optimizing processes. Greater visibility allows for better decision-making and more proactive management of the supply chain.
Ways to Enhance Visibility:
Real-Time Tracking: Implement tracking systems to monitor the movement and condition of goods in real-time.
Data Sharing: Encourage data sharing among all supply chain partners to ensure everyone has access to accurate and timely information.
Predictive Analytics: Use predictive analytics to forecast demand and manage inventory more effectively.
4. Enhancing Supply Chain Integration through Collaboration, Lean Principles, and Flexibility
Collaborative Planning and Forecasting
Collaborative planning and forecasting involve working closely with supply chain partners to develop accurate demand forecasts and production plans. This collaboration helps align supply chain activities with market demands, ensuring that all parties are on the same page regarding expectations and requirements.
Steps for Collaborative Planning:
Joint Demand Forecasting: Effective collaborative planning begins with joint demand forecasting. By working together, businesses and their supply chain partners can create shared demand forecasts based on historical data and current market trends. This collaboration allows for more accurate predictions and helps prevent the discrepancies that can occur when each party operates independently. Sharing information about market trends, seasonal variations, and promotional activities ensures that forecasts are realistic and comprehensive.
Synchronized Production Schedules: Aligning production schedules with demand forecasts is crucial for avoiding overproduction and stockouts. By synchronizing their production schedules, supply chain partners can ensure that manufacturing processes are aligned with actual market demand. This alignment reduces excess inventory and the associated carrying costs while also preventing shortages that can lead to missed sales opportunities and dissatisfied customers.
Integrated Inventory Management: Coordinating inventory management across the supply chain ensures optimal stock levels and reduces the risk of overstocking or stockouts. Integrated inventory management involves sharing real-time inventory data among all supply chain partners. This visibility allows for more accurate inventory planning and helps prevent situations where one partner runs out of stock while another has surplus inventory. By integrating inventory management, businesses can optimize their stock levels, reduce carrying costs, and improve overall supply chain efficiency.
Implementing Lean Principles
Lean principles focus on eliminating waste and optimizing processes to improve efficiency. Applying lean principles to supply chain management can lead to significant cost savings and performance improvements.
Lean Strategies for Supply Chain:
Value Stream Mapping: Value stream mapping involves identifying and mapping all activities in the supply chain to pinpoint areas of waste and inefficiency. This process helps businesses understand how value flows through their supply chain and where bottlenecks or unnecessary steps may exist. By visualizing the entire supply chain process, companies can identify opportunities for improvement and streamline their operations.
Continuous Improvement: Fostering a culture of continuous improvement is essential for maintaining and enhancing supply chain efficiency. Continuous improvement involves regularly evaluating and refining supply chain processes to eliminate waste and enhance performance. This approach encourages employees at all levels to identify areas for improvement and implement changes that drive efficiency and effectiveness.
Just-In-Time (JIT) Inventory: Implementing JIT inventory systems reduces holding costs and minimizes waste by aligning inventory levels with actual demand. JIT involves ordering and receiving goods only as they are needed for production or sales, reducing the need for large inventory holdings. This approach helps businesses respond more quickly to changes in demand and reduces the risk of overproduction and excess inventory.
Enhancing Flexibility and Responsiveness
An integrated supply chain must be flexible and responsive to changes in demand, market conditions, and external disruptions. Flexibility ensures that the supply chain can adapt quickly and maintain operational continuity.
Strategies for Enhancing Flexibility:
Agile Supply Chain Practices: Adopting agile supply chain practices allows businesses to make rapid adjustments to their supply chain activities in response to changing conditions. Agile practices involve maintaining flexible production processes, developing responsive logistics strategies, and fostering a culture of quick decision-making. This approach enables businesses to respond promptly to market fluctuations, customer demands, and unforeseen disruptions.
Diversified Supplier Base: Developing a diverse supplier base mitigates risks associated with supplier disruptions. Relying on a single supplier can be risky, as any disruption to that supplier's operations can impact the entire supply chain. By establishing relationships with multiple suppliers, businesses can reduce their vulnerability to disruptions and ensure a more stable supply of goods and materials.
Contingency Planning: Creating contingency plans to address potential disruptions is crucial for maintaining supply chain continuity. Contingency planning involves identifying potential risks, developing response strategies, and establishing protocols for communication and action. By preparing for various scenarios, businesses can minimize the impact of disruptions and maintain operational continuity.
Integrating the supply chain through collaborative planning and forecasting, lean principles, and enhanced flexibility and responsiveness is essential for businesses looking to optimize their operations and remain competitive in today's dynamic market environment. By working closely with supply chain partners, eliminating waste, and adopting flexible practices, companies can achieve greater efficiency, reduce costs, and improve customer satisfaction. Embracing these strategies will position businesses for long-term success and resilience in the face of ever-changing market demands and challenges.
Integrated supply chain management is essential for businesses looking to enhance efficiency, reduce costs, and improve customer satisfaction. By establishing strong partnerships, leveraging technology, enhancing visibility, collaborating on planning and forecasting, implementing lean principles, and enhancing flexibility, businesses can achieve a seamlessly integrated supply chain. Despite the challenges, the benefits of an integrated supply chain make it a worthwhile investment for any business aiming to stay competitive in today's dynamic market environment. Embracing these strategies will not only improve operational performance but also position businesses for long-term success.
