Inventory Management KPIs and Metrics
Discover the key to successful inventory management with our guide on essential KPIs and metrics – your roadmap to operational efficiency and customer satisfaction.
SUPPLY CHAIN
The Procure 4 Marketing Team
1/24/20246 min read
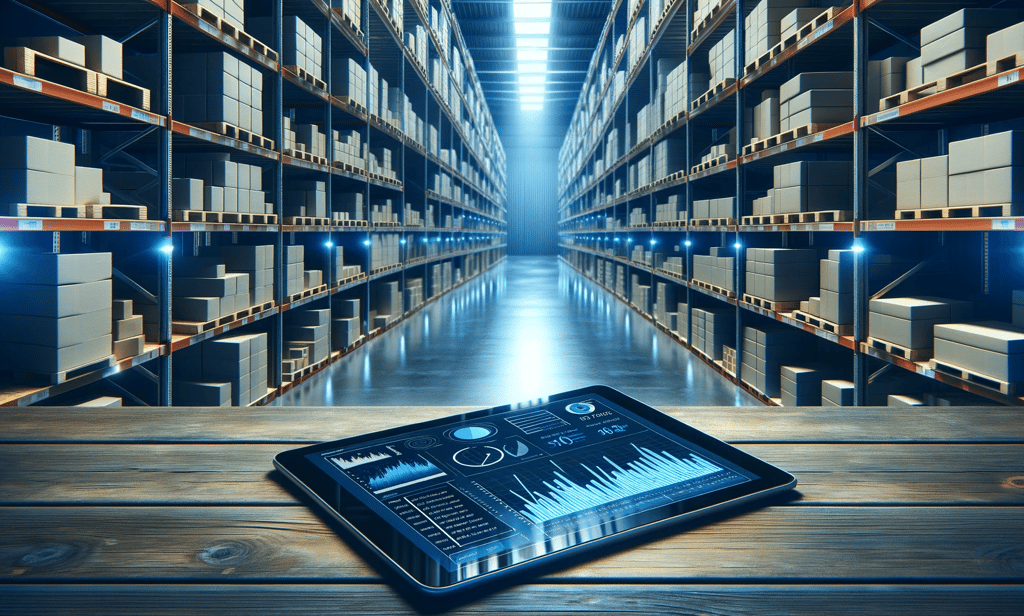
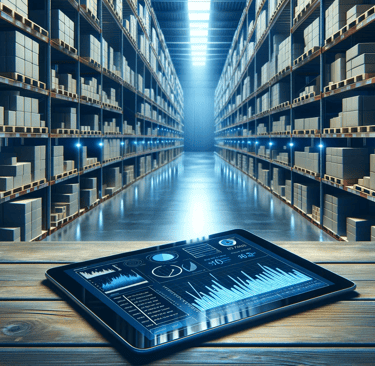
In the complex landscape of inventory management, Key Performance Indicators (KPIs) and metrics serve as essential tools, providing clarity and direction for effective inventory oversight. This introduction sets the stage for understanding their critical role and the importance of measuring inventory performance.
Deciphering the Role of KPIs and Metrics
Navigational Tools: KPIs and metrics in inventory management are akin to navigational aids, guiding businesses in tracking, analyzing, and optimizing their inventory processes. They are not just measurements but insights into the health and efficiency of inventory systems.
Strategic Decision-Making: These tools aid in making informed strategic decisions, from fine-tuning purchasing schedules to optimizing stock levels, ensuring that businesses can respond swiftly to market demands and internal needs.
The Imperative of Measuring Inventory Performance
Assessing Efficiency and Profitability: Regular measurement of inventory performance through KPIs and metrics is vital for assessing operational efficiency and overall profitability. It helps in identifying areas that require attention and improvement.
Adapting to Market Changes: In a rapidly changing market, these measurements enable businesses to adapt their inventory strategies effectively, maintaining a balance between meeting customer demands and minimizing costs.
As we delve deeper into inventory management KPIs and metrics, it’s clear that understanding and effectively utilizing these tools is crucial for maintaining a robust and responsive inventory system. They are indispensable for continuous improvement and strategic alignment in inventory management.
Key Inventory Management KPIs
Crucial Metrics for Optimal Inventory Management
Effective inventory management hinges on monitoring key performance indicators (KPIs) that reflect the health and efficiency of inventory practices. Among these, the Inventory Turnover Ratio, Days Sales of Inventory (DSI), and Gross Margin Return on Investment (GMROI) stand out as essential metrics.
Inventory Turnover Ratio
Indicator of Efficiency: This ratio measures how often inventory is sold and replaced over a certain period. A higher turnover indicates efficient management, suggesting that inventory is not sitting idle and is aligned with sales patterns.
Formula: It’s calculated by dividing the cost of goods sold by the average inventory.
Days Sales of Inventory (DSI)
Measuring Liquidity: DSI indicates the average number of days it takes for inventory to be sold. A lower DSI suggests a quicker conversion of inventory into sales, which is generally favorable.
Calculation: It’s determined by dividing the ending inventory by the cost of goods sold, then multiplying by the number of days in the period.
Gross Margin Return on Investment (GMROI)
Profitability Metric: GMROI assesses the profit earned for every dollar invested in inventory. It helps in understanding the financial return provided by inventory investment.
Formula: GMROI is calculated by dividing the gross margin by the average inventory cost.
These KPIs provide invaluable insights into inventory efficiency, liquidity, and profitability. By regularly monitoring these metrics, businesses can make informed decisions to optimize their inventory management strategies.
Operational Metrics for Inventory Management
Key Indicators for Streamlining Inventory Operations
Operational metrics in inventory management play a vital role in ensuring smooth, efficient, and responsive inventory processes. Among the most critical are Stock Accuracy, Order Lead Time, and Backorder Rate, each offering unique insights into the operational health of inventory management.
Stock Accuracy
Precision in Inventory Levels: Stock accuracy refers to the degree to which the actual inventory matches the recorded inventory levels. High accuracy is crucial for reliable planning and customer service.
Impact: Accurate stock levels prevent overstocking, reduce carrying costs, and minimize the risk of stockouts, directly impacting customer satisfaction and operational efficiency.
Order Lead Time
Measuring Responsiveness: This metric measures the time taken from when an order is placed until it is received and available for sale or use. It's essential for evaluating the efficiency of the supply chain.
Significance: Shorter lead times indicate a more responsive and agile inventory system, essential for meeting customer demands promptly.
Backorder Rate
Indicator of Stockouts: The backorder rate measures the percentage of orders that cannot be fulfilled due to insufficient stock. It’s a critical metric for assessing the effectiveness of inventory management.
Implications: A high backorder rate can signal issues in demand forecasting or replenishment practices and can negatively impact customer satisfaction and loyalty.
These operational metrics provide valuable insights into the efficiency and responsiveness of inventory management practices. Regular monitoring and improvement of these metrics are crucial for maintaining an effective and customer-centric inventory system.
Financial Metrics in Inventory Management
Evaluating the Fiscal Health of Inventory Practices
In inventory management, financial metrics are crucial for assessing the economic impact of inventory practices. Three key metrics – Carrying Cost of Inventory, Inventory to Sales Ratio, and Inventory Shrinkage – provide insights into the financial efficiency of inventory management.
Carrying Cost of Inventory
Assessing Storage Expenses: This metric represents the total cost of holding inventory, including storage, insurance, taxes, and opportunity costs. It's crucial for understanding the financial burden of stored goods.
Optimization Goal: Lowering these costs without compromising inventory availability is a common objective, striking a balance between cost savings and operational efficiency.
Inventory to Sales Ratio
Measuring Inventory Effectiveness: This ratio compares the amount of inventory a business has on hand to the number of sales being made. It helps gauge whether a company has too much inventory compared to its sales.
Indicator of Demand Alignment: Ideally, this ratio should align with industry norms and market demand, indicating effective inventory management.
Inventory Shrinkage
Tracking Inventory Loss: Shrinkage refers to the loss of inventory due to factors like theft, damage, or administrative errors. It's a critical metric for understanding the effectiveness of inventory control and security measures.
Reduction Strategies: Minimizing shrinkage is key to maintaining profitability and accurate inventory records.
These financial metrics are essential for evaluating the economic aspects of inventory management. Regularly monitoring these metrics helps businesses optimize their inventory practices, ensuring fiscal responsibility and operational effectiveness.
Using KPIs and Metrics for Strategic Decision-Making
Leveraging Data for Informed Inventory Management
The strategic use of KPIs and metrics in inventory management is crucial for making informed decisions that balance efficiency and customer satisfaction. Analyzing trends through these metrics guides businesses in refining their inventory strategies.
Data-Driven Insights: By analyzing trends in KPIs and metrics, businesses can identify patterns and anomalies in inventory management. This insight allows for proactive adjustments to stocking strategies, demand forecasting, and replenishment methods.
Balancing Act: The goal is to strike a balance between maintaining lean inventory levels to reduce costs and ensuring sufficient stock to meet customer demand. This balance is crucial for optimizing both operational efficiency and customer satisfaction.
Strategic Adjustments: Regular analysis of these metrics enables businesses to make strategic decisions, such as identifying the need for technological upgrades, adjusting procurement practices, or revising supplier contracts, all aimed at enhancing inventory management effectiveness.
Challenges in Measuring Inventory Performance
Navigating Obstacles in Effective Inventory Assessment
Measuring inventory performance accurately is crucial, yet it presents significant challenges that can impact the effectiveness of inventory management strategies. The primary hurdles include ensuring data accuracy and consistency and interpreting and acting on the metrics effectively.
Data Accuracy and Consistency: Accurate and consistent data collection is foundational for reliable inventory metrics. Inaccuracies in data entry, delays in updating information, and discrepancies between physical stock and system records can skew results, leading to misguided decisions.
Interpreting and Acting on Metrics: Understanding and correctly interpreting inventory metrics is another challenge. Misinterpretation can lead to incorrect conclusions and actions. Furthermore, translating these insights into actionable strategies requires not only understanding the data but also having the ability to implement effective changes in response to these insights.
Technology’s Role in Tracking KPIs and Metrics
Empowering Inventory Management with Advanced Tools
Technology plays a pivotal role in tracking and analyzing inventory management KPIs and metrics, offering precision and real-time insights that are essential for effective decision-making.
Inventory Management Software and Analytics Tools: Modern inventory management software comes equipped with analytics tools that automatically track and analyze key metrics. These tools offer detailed insights into inventory turnover, demand patterns, and efficiency, enabling more accurate forecasting and planning.
Real-Time Data Tracking and Reporting: The capability to track inventory data in real-time is a significant technological advancement. This allows businesses to respond quickly to changes in inventory levels, demand fluctuations, and supply chain disruptions, ensuring more agile and responsive inventory management. Real-time reporting enables immediate analysis and decision-making, crucial for maintaining optimal inventory levels and operational efficiency.
The Vital Role of KPIs and Metrics in Inventory Management
Cementing the Foundation for Strategic Inventory Oversight
As we wrap up our exploration of KPIs and metrics in inventory management, the undeniable value they bring to the table in driving effective and efficient inventory strategies becomes clear. These tools are not just indicators of performance; they are the compass guiding businesses towards operational excellence.
Reiterating the Importance of KPIs and Metrics
Key to Strategic Decision-Making: KPIs and metrics in inventory management are crucial for making informed decisions. They provide a quantifiable measure of how well inventory is managed, highlighting areas of success and pinpointing opportunities for improvement.
Balancing Efficiency with Customer Satisfaction: These measurements help in striking the delicate balance between maintaining optimal inventory levels, minimizing costs, and ensuring customer satisfaction. They enable businesses to respond proactively to market changes and consumer demands.
Encouraging Continuous Improvement
Evolving with Market Dynamics: The landscape of inventory management is continually evolving. Hence, it’s vital for businesses to keep updating and refining their approach to measuring inventory performance. This includes adopting new technologies, embracing more sophisticated analytics methods, and adjusting KPIs to align with changing business objectives.
Commitment to Best Practices: Continuous improvement in inventory performance measurement is not just about using the right tools but also about a commitment to best practices. It involves regular training, staying abreast of industry trends, and fostering a culture of agility and responsiveness.
In conclusion, KPIs and metrics play an indispensable role in the realm of inventory management. They are the linchpins that ensure businesses can navigate the complexities of inventory management effectively, driving operational success and customer satisfaction. Businesses are encouraged to continually hone their measurement strategies, embracing technological advancements and best practices for a more insightful and dynamic approach to inventory management.
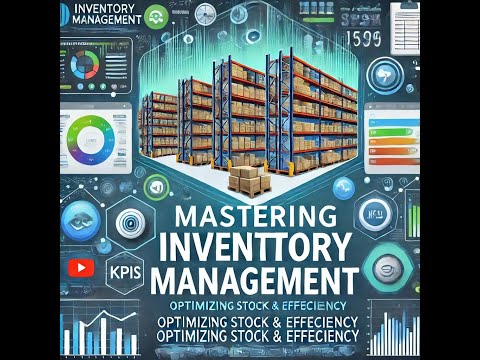