Collaborative Supply Chain Models
Discover the benefits of collaborative supply chain models to enhance efficiency, reduce costs, and improve customer satisfaction through strategic partnerships and data sharing.
SUPPLY CHAIN
The Procure 4 Marketing Team
6/26/20246 min read
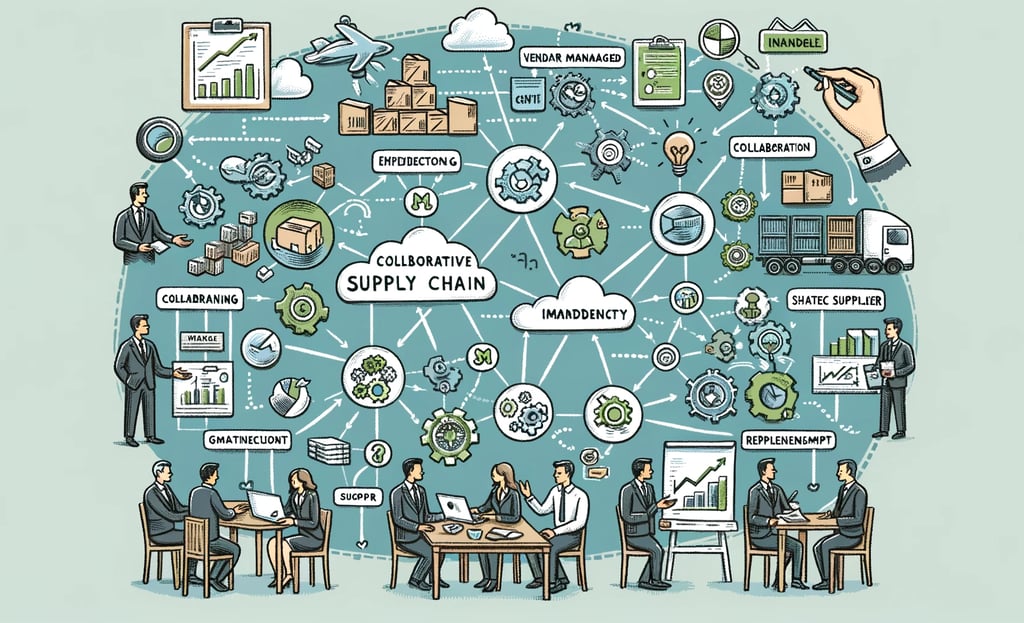

Collaborative supply chain models emphasize the importance of cooperation and coordination among supply chain partners to achieve greater efficiency, cost savings, and customer satisfaction. In an increasingly interconnected and globalized market, businesses can no longer operate in silos. Instead, they must work closely with suppliers, manufacturers, distributors, and customers to create a seamless and integrated supply chain. This post will explore various collaborative supply chain models, their benefits, and strategies for successful implementation.
Importance of Collaborative Supply Chain Models
Collaborative supply chain models offer numerous advantages:
Enhanced Efficiency: By synchronizing activities and sharing information, supply chain partners can eliminate redundancies and streamline operations.
Cost Savings: Collaborative efforts can lead to bulk purchasing, shared resources, and optimized logistics, all of which contribute to cost reductions.
Improved Customer Satisfaction: A well-coordinated supply chain can better respond to customer needs, ensuring timely deliveries and high-quality products.
Key Collaborative Supply Chain Models
1. Vendor Managed Inventory (VMI)
Vendor Managed Inventory (VMI) is a collaborative supply chain model in which the supplier assumes responsibility for managing inventory levels at the customer’s location. This arrangement fosters close collaboration between suppliers and customers, ensuring that inventory levels are optimized and the risk of stockouts is minimized.
Benefits of VMI:
Inventory Optimization: Suppliers utilize real-time data to maintain optimal inventory levels. This reduces the risk of overstocking, which can tie up capital, and stockouts, which can lead to missed sales and dissatisfied customers.
Cost Reduction: By minimizing inventory holding costs and improving order accuracy, VMI can lead to significant cost savings. Efficient inventory management reduces the need for excessive safety stock and lowers warehousing costs.
Improved Service Levels: With better insights into customer needs, suppliers can anticipate demand more accurately and ensure timely replenishments. This leads to higher service levels, increased customer satisfaction, and stronger supplier-customer relationships.
Strategies for Implementing VMI:
Data Sharing: Establish robust systems for real-time data sharing between suppliers and customers. This transparency ensures that both parties have access to accurate inventory levels and demand forecasts.
Performance Metrics: Develop shared performance metrics to track the effectiveness of the VMI program. Metrics might include inventory turnover rates, stockout incidents, and order accuracy.
Trust and Communication: Build strong relationships based on trust and open communication. Regular meetings, updates, and collaborative problem-solving are essential to ensure successful collaboration and continuous improvement in the VMI program.
By effectively implementing VMI, businesses can achieve more efficient inventory management, cost savings, and improved service levels, ultimately leading to a more responsive and resilient supply chain.
2. Collaborative Planning, Forecasting, and Replenishment (CPFR)
Collaborative Planning, Forecasting, and Replenishment (CPFR) is a model that involves joint planning and forecasting between supply chain partners to ensure that supply aligns with demand. CPFR emphasizes shared data, joint decision-making, and synchronized activities across the supply chain.
Benefits of CPFR:
Accurate Forecasting: By pooling data and insights from all supply chain partners, CPFR enables the creation of more accurate demand forecasts. This collaborative approach reduces the uncertainty that often accompanies individual forecasting efforts.
Aligned Operations: Joint planning ensures that production, inventory, and logistics activities are synchronized with actual market demand. This alignment helps to avoid the pitfalls of overproduction or underproduction, leading to more efficient operations.
Reduced Inventory Levels: Improved forecasting and planning can lead to lower inventory levels and reduced carrying costs. Accurate demand predictions allow for more precise inventory management, minimizing the need for large safety stocks and reducing associated storage costs.
Steps for Implementing CPFR:
Collaborative Planning: Engage in joint planning sessions to align strategies and objectives. These sessions should include representatives from all relevant supply chain partners to ensure comprehensive and cohesive planning.
Data Integration: Integrate data systems to enable seamless sharing of information. This integration ensures that all partners have access to up-to-date and accurate data, facilitating informed decision-making.
Regular Reviews: Conduct regular reviews to assess performance and make necessary adjustments. These reviews should evaluate the accuracy of forecasts, the efficiency of replenishment processes, and the overall effectiveness of the CPFR initiative.
By implementing CPFR, businesses can achieve greater accuracy in demand forecasting, better alignment of supply chain activities, and reduced inventory levels, leading to improved efficiency and cost savings across the supply chain.
3. Strategic Supplier Partnerships
Strategic supplier partnerships involve long-term collaborations between businesses and their key suppliers. These partnerships transcend mere transactional relationships, emphasizing mutual growth, innovation, and continuous improvement. Such strategic alliances are critical for creating a resilient and efficient supply chain.
Benefits of Strategic Supplier Partnerships:
Innovation: Close collaboration fosters innovation and the development of new products and solutions. By working together, businesses and suppliers can leverage each other's expertise and resources to drive innovation, improve product quality, and respond quickly to market changes.
Risk Mitigation: Long-term partnerships help mitigate risks associated with supply disruptions. A stable, reliable relationship with key suppliers ensures better communication and coordination, reducing the likelihood of unexpected interruptions and enabling quicker recovery from disruptions.
Cost Savings: Joint initiatives, such as bulk purchasing and process improvements, can lead to significant cost reductions. These collaborations can optimize supply chain processes, reduce waste, and enhance efficiency, ultimately lowering overall costs.
Strategies for Building Strategic Supplier Partnerships:
Mutual Goals: Establish shared goals and objectives to ensure alignment. Both parties should agree on common targets, such as quality standards, delivery schedules, and sustainability practices, to ensure their efforts are coordinated and mutually beneficial.
Regular Communication: Maintain open lines of communication through regular meetings and updates. Effective communication fosters transparency, trust, and swift problem-solving, helping both parties stay aligned and informed about each other’s needs and capabilities.
Performance Metrics: Develop and track performance metrics to monitor progress and identify areas for improvement. These metrics might include delivery performance, quality standards, and cost savings. Regularly reviewing these metrics helps ensure that the partnership is meeting its objectives and allows for continuous improvement.
Strategic supplier partnerships are essential for fostering innovation, mitigating risks, and achieving cost savings. By focusing on mutual goals, maintaining regular communication, and tracking performance metrics, businesses can build strong, long-lasting relationships with their suppliers that drive growth and success.
4. Co-Managed Inventory (CMI)
Co-Managed Inventory (CMI) is a collaborative supply chain model where both the supplier and the customer share the responsibility for managing inventory levels. This approach merges the advantages of Vendor Managed Inventory (VMI) with traditional inventory management, promoting collaboration while allowing both parties to retain control over inventory decisions.
Benefits of CMI:
Flexibility: CMI allows both the supplier and the customer to make inventory decisions based on real-time data and changing market conditions. This adaptability ensures that inventory levels are optimized to meet current demand and supply scenarios.
Improved Responsiveness: Joint management facilitates quick responses to demand fluctuations and supply chain disruptions. By sharing real-time information, both parties can react promptly to unexpected changes, ensuring continuity and minimizing downtime.
Cost Efficiency: Shared responsibility in inventory management can lead to optimized inventory levels and reduced costs. By collaborating, suppliers and customers can minimize excess inventory, reduce holding costs, and improve order accuracy.
Strategies for Implementing CMI:
Joint Data Sharing: Implement systems for real-time data sharing and communication. This transparency ensures that both parties have access to up-to-date information on inventory levels, demand forecasts, and supply chain status, enabling informed decision-making.
Clear Roles and Responsibilities: Define roles and responsibilities to ensure clarity and accountability. Both parties should understand their specific duties and how they contribute to overall inventory management, fostering a collaborative environment while maintaining clear lines of accountability.
Performance Monitoring: Regularly monitor performance metrics to ensure the effectiveness of the CMI program. Key metrics might include inventory turnover rates, stockout incidents, and order fulfillment times. Regular reviews of these metrics help identify areas for improvement and ensure that the CMI model delivers the expected benefits.
By effectively implementing CMI, businesses can achieve greater flexibility, responsiveness, and cost efficiency in their inventory management, resulting in a more resilient and optimized supply chain.
Challenges and Considerations
While collaborative supply chain models offer numerous benefits, they also present challenges that businesses must address:
Data Security: Sharing sensitive data requires robust security measures to protect against breaches and unauthorized access.
Integration Complexity: Integrating systems and processes across multiple organizations can be complex and resource intensive.
Cultural Differences: Differences in organizational culture and practices can hinder collaboration efforts.
Trust and Transparency: Building trust and maintaining transparency are critical for successful collaboration, requiring ongoing effort and commitment.
Collaborative supply chain models are essential for businesses looking to optimize their operations, reduce costs, and enhance customer satisfaction. By adopting models such as Vendor Managed Inventory, Collaborative Planning, Forecasting, and Replenishment, Strategic Supplier Partnerships, and Co-Managed Inventory, companies can achieve greater efficiency and responsiveness in their supply chains. However, successful implementation requires careful planning, robust data sharing systems, and a commitment to building strong, trust-based relationships with supply chain partners. Embracing these collaborative models will position businesses for long-term success and resilience in an increasingly competitive and dynamic market environment.
