ABC Analysis in Inventory Management
Discover how ABC Analysis optimizes inventory management, balancing costs, and strategic alignment for business efficiency.
SUPPLY CHAIN
The Procure 4 Marketing Team
2/14/20247 min read
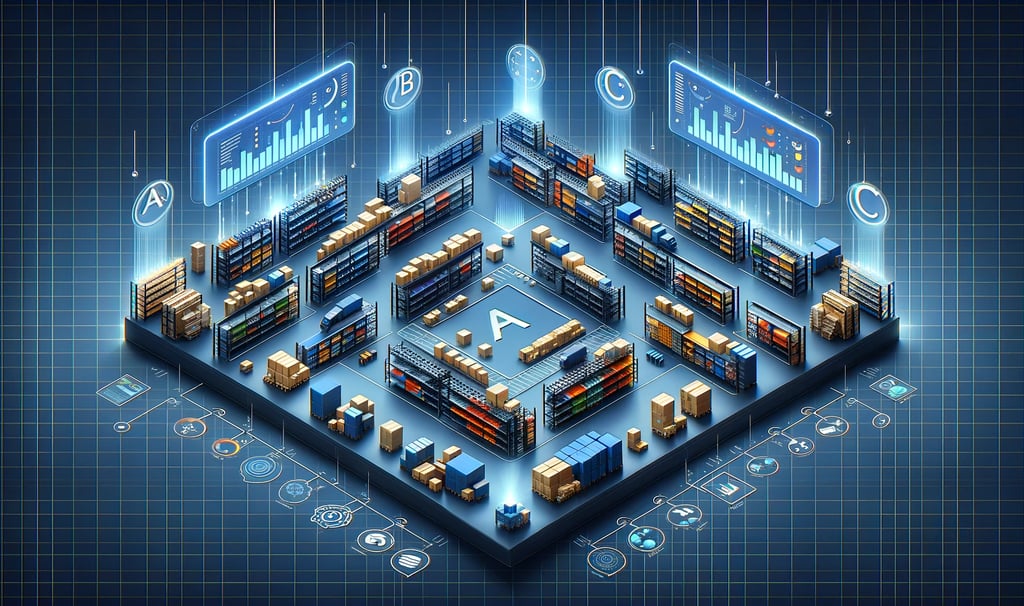
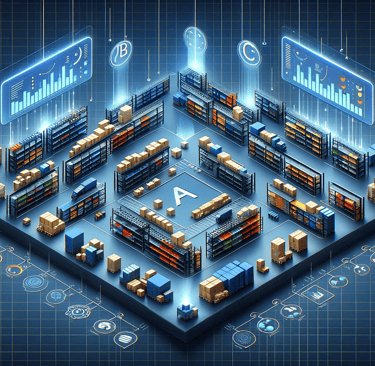
Welcome to the insightful world of ABC Analysis in Inventory Management, a method pivotal for streamlining inventory and enhancing operational efficiency. This introduction lays the foundation for understanding ABC analysis and underscores the importance of strategic inventory categorization.
1- Defining ABC Analysis
ABC analysis is an inventory categorization technique used to prioritize items based on their significance to the business. It segments inventory into three categories: 'A' for high-value, low-frequency items; 'B' for moderate-value, moderate-frequency items; and 'C' for low-value, high-frequency items.
This method typically involves ranking inventory based on criteria like annual consumption value, cost significance, or turnover rates, allowing businesses to focus more on items that require closer management and control.
The Importance of Inventory Categorization
Optimizing Resources: Effective categorization helps businesses allocate resources efficiently, focusing time and effort on managing items that have the greatest impact on inventory costs and business operations.
Enhanced Inventory Control: By identifying which items are most crucial, ABC analysis aids in better stock control, preventing overstocking or stockouts, and ultimately improving overall inventory management.
ABC analysis serves as a key tool in the realm of inventory management, providing a structured approach to categorize and manage inventory effectively. Understanding its fundamentals is essential for businesses looking to optimize their inventory processes and decision-making strategies.
2- Understanding ABC Analysis
ABC analysis stands as a fundamental approach in inventory management, providing a systematic method for categorizing inventory into three distinct groups based on specific criteria. This categorization aids in prioritizing management efforts and resource allocation.
The Principle of ABC Analysis
Three-Tier Categorization: At its core, ABC analysis divides inventory into three categories. 'A' items are typically high in value but low in quantity, making up a significant portion of inventory value. 'B' items are of moderate value and quantity, and 'C' items, while high in quantity, are low in value.
Focus Based on Category: This categorization allows businesses to focus more attention and resources on 'A' items, which are crucial to the business's success, while managing 'B' and 'C' items with proportionally less effort.
Criteria for Categorizing Items
Value-Based Segmentation: Items are often categorized based on their monetary value, with high-value items falling into the 'A' category.
Turnover Rate and Criticality: Other factors for categorization include turnover rate and the criticality of items to production or sales processes. High turnover or critical items might be classified as 'A' even if their individual value is lower, due to their importance in maintaining business operations.
ABC analysis provides a structured approach to inventory management, allowing businesses to prioritize their focus and resources effectively based on the value, turnover rate, and criticality of different inventory items.
3- Benefits of Implementing ABC Analysis
Adopting ABC analysis in inventory management offers numerous benefits, enhancing overall efficiency and effectiveness. This strategic approach streamlines processes, focuses efforts on crucial items, and contributes to cost savings.
Improved Inventory Control and Efficiency
Targeted Management: By categorizing inventory into A, B, and C groups, businesses can allocate their attention and resources more effectively. High-priority 'A' items receive the most attention, ensuring critical stock levels are always optimal.
Streamlined Operations: This prioritization leads to more efficient operations, as time and resources are not wasted on managing low-value items with the same intensity as high-value ones.
Enhanced Focus on High-Value Items
Prioritizing Critical Inventory: ABC analysis ensures that high-value or critical items (Category A) are closely monitored and managed, reducing the risk of stockouts that could significantly impact business operations.
Data-Driven Decisions: This method allows for more informed decision-making regarding purchasing, storing, and replenishing inventory based on value and utility.
Cost Savings and Reduced Waste
Optimizing Inventory Levels: By focusing on the most important items, businesses can keep tighter control over inventory levels, reducing the costs associated with excess stock, such as storage and insurance.
Minimizing Waste: Efficient management of high-turnover items (often in categories B and C) reduces the likelihood of obsolescence and waste, contributing to overall cost savings.
Implementing ABC analysis in inventory management leads to more precise control, a keen focus on high-value items, and significant cost savings. This approach fosters a more organized, efficient, and financially savvy inventory management system.
4- Steps to Conduct ABC Analysis
Implementing ABC analysis in inventory management involves a systematic process of data gathering, analysis, and categorization, leading to the creation of specific strategies for each category. Here are the key steps to conduct ABC analysis effectively:
Gathering and Analyzing Inventory Data
Data Collection: Start by collecting comprehensive data on all inventory items. This data should include sales volume, purchase costs, turnover rates, and any other relevant metrics.
Analytical Review: Analyze this data to understand the contribution of each item to overall inventory costs and turnover. This analysis forms the basis for categorizing items into different groups.
Categorizing Items into A, B, and C Groups
Applying Criteria: Based on the analysis, categorize the inventory items into three groups. 'A' items are high in value but low in quantity, 'B' items are moderate in both value and quantity, and 'C' items are low in value but high in quantity.
Percentage Allocation: Typically, 'A' items represent about 20% of inventory items but about 70-80% of the inventory value, 'B' items around 30% of items and 15-25% of value, and 'C' items the remaining 50% of items but only 5-10% of value.
Creating Strategies for Each Category
Tailored Strategies: Develop specific management strategies for each category. 'A' items require close monitoring and strict control, 'B' items moderate attention, and 'C' items the least rigorous control.
Continuous Review: Regularly review the categorization and adjust the strategies as necessary to reflect changes in the inventory or market conditions.
Conducting ABC analysis involves careful data analysis and strategic categorization, followed by the implementation of tailored strategies for each group. This process helps businesses optimize their inventory management, focusing resources where they are most needed.
5- Challenges in ABC Analysis
While ABC analysis is a valuable tool in inventory management, implementing it effectively presents certain challenges. Key among these are managing category overlaps and adapting the analysis to evolving business needs.
Managing Category Overlaps and Exceptions
Overlap Issues: One of the main challenges in ABC analysis is dealing with items that don't fit neatly into a single category. Items may have characteristics that qualify them for multiple categories, leading to confusion in prioritization and management.
Handling Exceptions: Exceptional items, such as those with seasonal demand spikes or critical items with irregular usage, may not conform to the standard ABC categorization, necessitating a more nuanced approach.
Adapting the Analysis to Changing Business Needs
Dynamic Business Environments: In rapidly changing business environments, the relevance of ABC categorization can shift. What was a 'B' category item last quarter could become an 'A' category item due to changes in demand, market conditions, or supply chain dynamics.
Regular Reassessment: Continually reassessing the categorization of items is necessary to ensure that the ABC analysis remains aligned with current business realities and inventory needs.
Successfully implementing ABC analysis requires not only understanding its principles but also skillfully managing category overlaps and regularly adapting the analysis to reflect changing business scenarios. Addressing these challenges is crucial for maintaining an effective and responsive inventory management system.
6- Integrating ABC Analysis with Other Inventory Techniques
Effectively blending ABC analysis with other inventory management techniques can lead to a more holistic and efficient approach. Here's how ABC analysis can be integrated with methods like Just-In-Time (JIT), Economic Order Quantity (EOQ), and the role of technology in enhancing this process.
Combining ABC Analysis with JIT and EOQ
With JIT: ABC analysis can be aligned with JIT principles by focusing on 'A' category items for just-in-time restocking, ensuring high-value items are available as needed without overstocking.
With EOQ: The EOQ model can be applied differently for each ABC category. For 'A' items, a more precise EOQ calculation is warranted due to their high impact, while a more flexible approach can be adopted for 'B' and 'C' items.
The Role of Technology in Enhancing ABC Analysis
Data Analytics: Advanced software and data analytics tools can streamline the categorization process in ABC analysis, providing real-time data and predictive analytics for better decision-making.
Integration with Inventory Systems: Integrating ABC analysis into existing inventory management systems helps in automating and updating categorization processes, ensuring that the ABC analysis remains relevant and accurate over time.
Integrating ABC analysis with other inventory management methods like JIT and EOQ, and leveraging technology for data analysis and system integration, can significantly enhance inventory efficiency. This comprehensive approach allows businesses to tailor their inventory strategies to specific product categories and changing market conditions.
7- Best Practices for ABC Analysis
For ABC analysis to be effective in inventory management, adherence to certain best practices is crucial. Regular reviews, updates, and customization to fit specific business contexts are key to maximizing its benefits.
Regular Review and Update of Categories
Dynamic Market Adaptation: Inventory categories in ABC analysis are not static. Regularly reviewing and updating these categories is essential to ensure they reflect current market trends, demand patterns, and business priorities.
Responsive Adjustments: As business needs and market conditions change, adjustments may be needed in categorization. This could involve moving items between categories as their sales volume or value changes.
Tailoring ABC Analysis to Specific Business Contexts
Custom Criteria Development: While typical ABC analysis criteria involve value and volume, businesses should develop criteria that align with their unique operational and strategic goals. This could include factors like lead time, criticality to production, or seasonality.
Context-Specific Strategies: Different business contexts may require different management strategies for each category. For instance, high-demand industries might focus more on the availability of 'A' items, while others might emphasize cost reduction in 'C' items.
Implementing ABC analysis effectively requires a tailored approach that takes into account the specific needs and contexts of the business. Regular reviews and updates, along with customization of categorization criteria and management strategies, are essential for leveraging the full potential of ABC analysis in inventory management.
Embracing ABC Analysis for Enhanced Inventory Management
Highlighting the Integral Role of ABC Analysis in Streamlined Inventory
As we conclude our exploration of ABC analysis in inventory management, its significance as a strategic tool for efficient and effective inventory control becomes unequivocally clear. This methodology not only simplifies inventory management but also aligns it with the broader business objectives.
Reaffirming the Significance of ABC Analysis
Strategic Inventory Prioritization: ABC analysis provides a structured approach to prioritizing inventory, ensuring that resources are focused on the most impactful items. This leads to better inventory control, reduced costs, and optimized resource allocation.
Adaptability and Precision: The categorization process inherent in ABC analysis adapts to various business needs, offering a customizable and precise approach to inventory management.
Encouraging the Adoption of ABC Analysis
A Tool for Efficiency and Growth: Businesses are encouraged to adopt ABC analysis as a key component of their inventory strategy. Its ability to differentiate inventory based on value and turnover rate makes it an invaluable asset in decision-making processes.
Tailored Approach for Diverse Industries: ABC analysis is versatile and can be tailored to suit different industries and business sizes. Its implementation can lead to significant improvements in managing inventory, irrespective of the scale or nature of the business.
In summary, ABC analysis stands out as a vital strategy in modern inventory management. Its adoption can significantly enhance the efficiency and effectiveness of inventory control, making it a recommended approach for businesses aiming to optimize their inventory practices and overall operational performance.
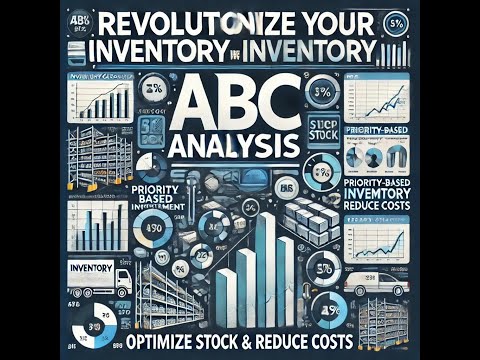